Standard Components of a Commercial Label
The main components that make up a label
- Coating / Topcoat / Laminate
- Ink / Printing
- Face Stock / Material
- Adhesive
- Liner / Backing
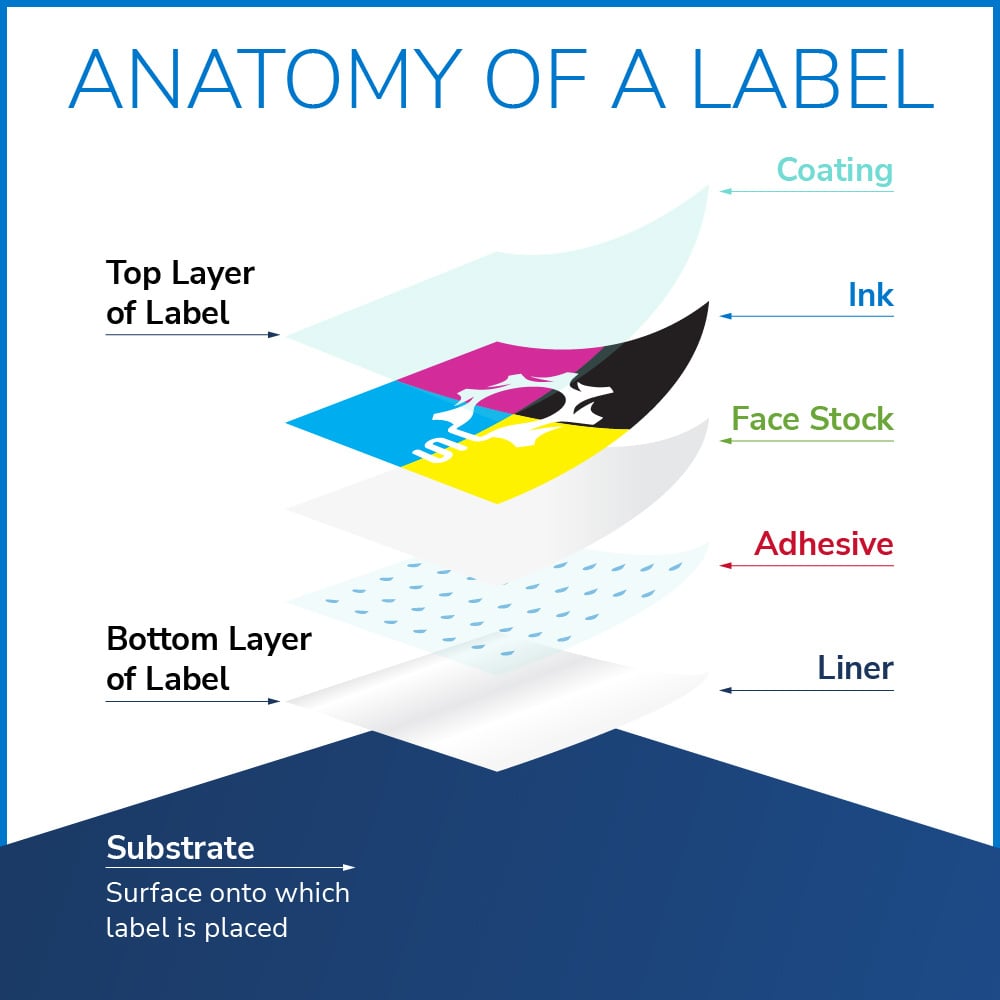
PRO TIP: Start with the Substrate!
When considering the application of a label, starting with the surface is crucial to achieving professional and long-lasting results.
The surface not only determines how well the label adheres but also influences its durability and effectiveness.
Whether you're labeling products, storage containers, or shipment packages, understanding the importance of surface preparation ensures the label remains intact and legible over time. Factors such as texture, cleanliness, and material composition can dramatically affect adhesion.
Coating / Topcoat / Laminate
A protective coating or film applied to the facestock to enhance durability and resist exposure to environmental factors like water, UV light, chemicals, or abrasion.
Function: Protects the printed surface from damage and extends the life of the label, especially in harsh environments.
Common Materials:
- UV Coating: Protects against sun exposure and fading.
- Gloss or Matte Laminate: Adds a protective layer that can also change the label’s finish (shiny or dull).
Ink / Printing
The layer where the information or design (text, images, logos) is printed onto the facestock. Different printing methods are used depending on the label’s application and the desired level of detail and durability.
Function: Conveys the information, branding, and messaging of the label.
Common Ink Types:- Water-Based Inks: Suitable for eco-friendly or cost-effective labeling.
- UV Inks: Cured with UV light for fast-drying and long-lasting results.
- Thermal Transfer Inks: Used for printing variable data (barcodes, batch numbers) in industrial settings.
Face Stock / Material
The top layer of the label displays printed information (text, images, barcodes). It is the visible part of the label and can be made of various materials, such as paper, film, vinyl, or polyester, depending on the application.
Function: Carries the printed design or information and is chosen based on durability, appearance, and suitability for the product or environment.
Common Materials:- Paper: Ideal for short-term or indoor use, often used for food packaging or retail.
- Film (Polypropylene, Polyester): Durable and resistant to water, chemicals, and UV exposure, making them suitable for outdoor or industrial use.
- Vinyl: Highly durable, used in harsh environments like automotive or industrial products.
Adhesive
The layer that bonds the facestock to the product or packaging. Different types of adhesives are available, depending on the application, surface, and whether the label needs to be permanent or removable.
Function: Ensures the label adheres securely to the product surface.
Types of Adhesives:- Permanent: Strong and long-lasting, designed to stay on the product for its entire life.
- Removable: Designed to be removed without damaging the surface or leaving residue.
- Freezer-Grade: Strong enough to adhere in cold temperatures, commonly used for frozen goods.
- Repositionable: Allows for repositioning the label before a permanent bond forms.
Optional Release Coating
A specialized layer applied to the surface of the release line (the backing) of a label to create a smooth, non-stick surface that allows the label to be easily peeled away without damaging the adhesive or label.
Function: Ensures the label backing can be removed cleanly.
Types of Materials: Silicone or similar non-stick materials.
Liner / Backing
A protective backing layer that covers the adhesive until the label is ready to be applied. It prevents the adhesive from sticking to other surfaces before use.
Function: Keeps the label intact during storage and transportation. It is peeled away to reveal the adhesive during application.
Common Materials:
- Silicone-Coated Paper: Common for general labels, offering easy release.
- Polyethylene or Polyester Film: Used for specialized labels that require more flexibility or durability during the release process.
Additional Considerations
Die-Cut (Shape)
The label’s shape or cut, created by a die-cutting process that forms the desired outline (round, square, custom shapes).
Function: Ensures the label fits the product or packaging shape properly.
Pro Tip: Custom die-cut shapes can enhance branding and visual appeal, making products stand out on shelves.
Overlaminate
Description: A clear, protective film applied over the label surface to add extra durability, making it resistant to scratches, moisture, or chemicals.
Function: Extends the life of the label, particularly for products exposed to harsh environments or frequent handling.
Perforations
Description: Small cuts or holes in the liner or label to allow easy separation of individual labels or sections of a larger label.
Function: Improves ease of use when applying labels in bulk or for peel-and-apply processes.